BATMAN 25 of 100
Created on: July 7th, 2012
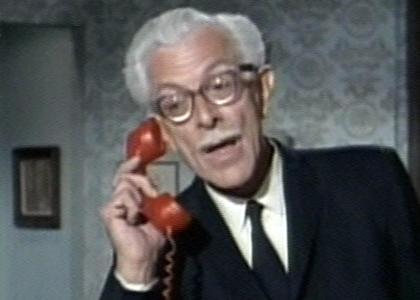
Sponsorships:
user | amount | user | amount |
---|---|---|---|
No one has sponsored this site ( ._.) | |||
Sponsor this site! | Total: $0.00 | Active: $0.00 |
Vote metrics:
rating | total votes | favorites | comments |
---|---|---|---|
(4.08) | 93 | 19 | 46 |
View metrics:
today | yesterday | this week | this month | all time |
---|---|---|---|---|
1 | 0 | 0 | 0 | 7,640 |
Inbound links:
views | url |
---|---|
60 | https://www.bing.com |
23 | http://www.stumbleupon.com/su/ |
6 | http://www.facebook.com/ |
5 | http://www.google.com.hk |
5 | https://www.google.ie/ |
28 µm thick piezoelectric PVDF polymer film with
screen-printed Ag-ink electrodes, laminated to a
0.125 mm polyester substrate, and fitted with two
crimped contacts. As the piezo film is displaced
from the mechanical neutral axis, bending creates
very high strain within the piezopolymer and
therefore high voltages are generated. When the
assembly is deflected by direct contact, the device
acts as a flexible "switch", and the generated
output is sufficient to trigger MOSFET or CMOS
stages directly. If the assembly is supported by its
contacts and left to vibrate "in free space" (with the
inertia of the clamped/free beam creating bending
stress), the device will behave as a form of
accelerometer or vibration sensor. Adding mass,
or altering the free length of the element by
clamping, can change the resonant frequency and
sensitivity of the sensor to suit specific
applications. Multi-axis response can be achieved by positioning the mass off center
Four different experiments serve to illustrate the various properties of this simple but versatile component.
1)LDT0 as Vibration Sensor - with the crimped contacts pushed through a printed-circuit board, the LDT0 was
soldered carefully in place to anchor the sensor. A charge amplifier was used to detect the output signal as
vibration from a shaker table was applied (using a charge amplifier allows a very long measurement time
constant and thus allows the "open-circuit" voltage response to be calculated). Small masses (approximately
0.26g increments) were then added to the tip of the sensor, and the measurement repeated. Results are
shown in Table 1 and the overlaid plots in Fig 1. Without adding mass, the LDT0 shows a resonance around
180 Hz. Adding mass to the tip reduces the resonance frequency and increases "baseline" sensitivity.
2)LDT0 as Flexible Switch - using a charge amplifier to obtain "open-circuit" voltage sensitivity, the output was
measured for controlled tip deflections applied to the sensor (supported by its crimped contacts as described
above). 2 mm deflection was sufficient to generate about 7 V. Voltages above 70V could be generated by
bending the tip of the sensor through 90° (see Table 2, Fig 2).
3)LDT0 Electrical Frequency Response - when the source capacitance of around 480 pF is connected to a
resistive input load, a high-pass filter characteristic results. Using an electronic noise source to generate broad-
band signals, the effect of various load resistances were measured and the -3 dB point of the R-C filter
determined (see Table 3, Fig 3).
4)LDT0 Clamped at Different Lengths - using simple clamping fixture, the vibration sensitivity was measured
(as in (1) above) as the clamp was moved to allow different "free" lengths to vibrate. The sensor may be
"tuned" to suit specific frequency response requirements (see Table 3, Fig 3).
Bold
Italic
Underline
Code
User Link
Site Link